Treatment specifications
This is a surfaces conversion of the same part to aluminum oxide and not a surface coating.
As a conversion, the layer formed penetrates half inside and half grows outside the part, developing evenly over the entire surface of the part.
Therefore, changes in elevation caused by the conversion of aluminum to oxide must be considered when designing the part.
In addition to its acquired work skills, Mochem can offer technical, chemical and metallurgical knowledge of the materials, combined with advice on any issues related to the construction of the part prior to treatment.
We classify oxidation as hard from 20-30 microns minimum, up to an optimum thickness of 45-50 microns (again depending on the alloy used).
Treatment features
COLORS
Hard anodizing is a self-coloring treatment: coloring can vary from gray to bronze to anthracite gray depending on the alloy used and the thickness required.
Because of the previously mentioned self-coloring, the only color that can be added to hard anodizing is black.
SUPPLEMENTARY TREATMENT
Hard anodizing process can be supplemented with PTFE (Teflon®) impregnation treatment: this simply penetrates into the pores of the oxide (without changing the dimensions), greatly improving the friction coefficient of the coating.
In addition, the PFTE treatment is considered non-toxic: it therefore allows the use of anodic treatment even on materials used in the food and pharmaceutical industries.
SPECIAL PROTECTION
Upon request, special protectors can be applied prior to treatment to shield a part of the component from anodization.
Depending on the surface or hole to be protected, different methods are used in order to achieve the customer’s requirements.
REGULATIONS COMPLIED WITH
– UNI 7796
– MIL A-8625F TYPE III
Maximum size of tanks
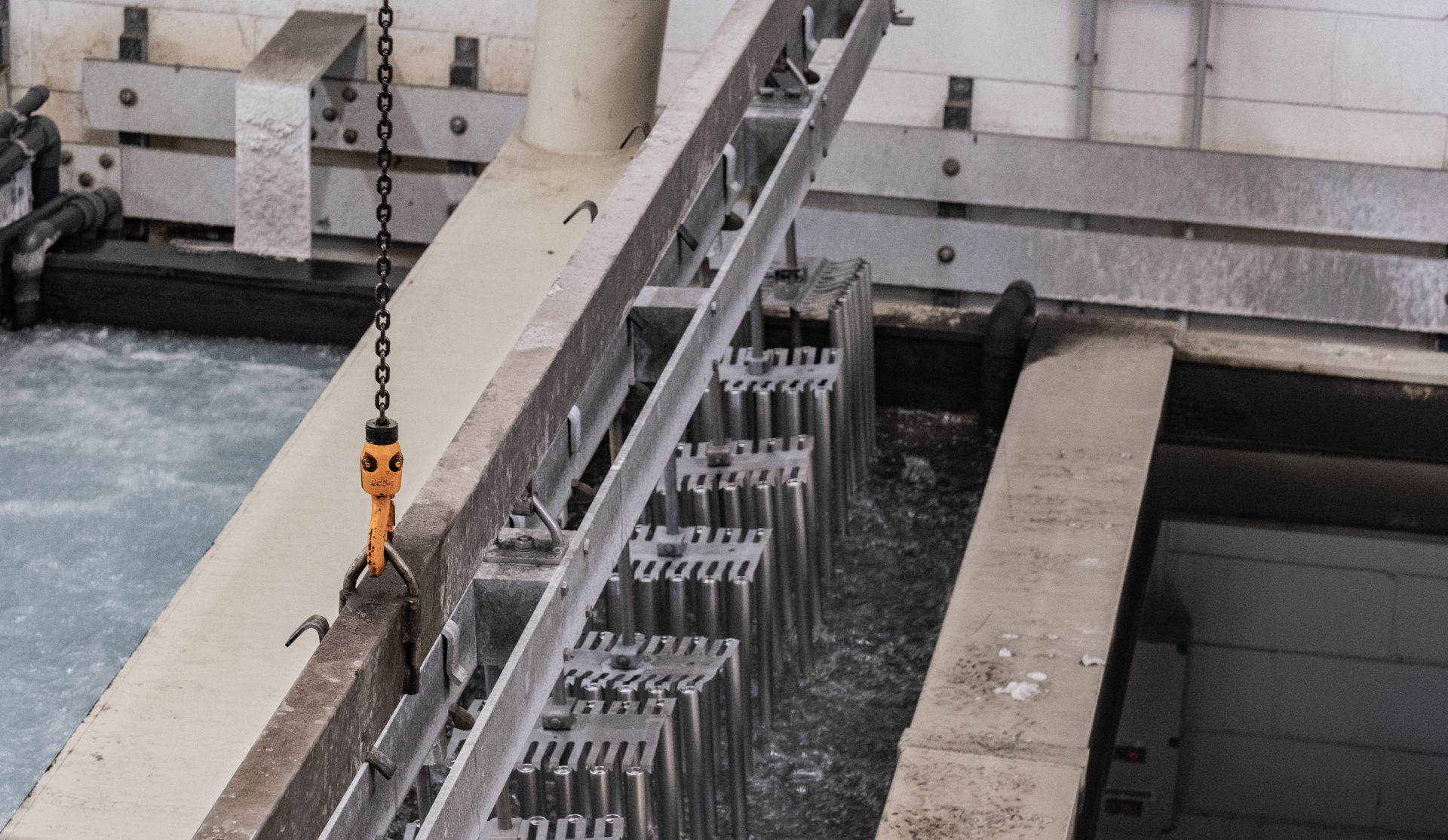
HARD ANODIZING WITHOUT BLACK COLOR
3700 x 1300 x 850 mm – max 500 Kg
3000 x 1500 x 500 mm – max 250 Kg
HARD ANODIZING WITH BLACK COLOR
3000 x 1500 x 500 mm – max 250 Kg
HARD ANODIZING WITH PTFE IMPREGNATION
3000 x 1500 x 500 mm – max 250 Kg
For details approaching maximum sizes and weights, please contact us or write to info@mochem.it.
WRITE TO US
Contact us for more information or to request a quote.
Fill out the form below and we will get back to you as soon as possible.